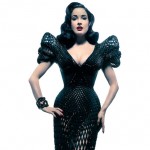
New York designer Michael Schmidt and architect Francis Bitonti have created a 3D-printed dress for burlesque dancer Dita Von Teese.
Images above and top by Albert Sanchez.
Designed by Schmidt and generated by Bitonti, the floor-length nylon gown was made using selective laser sintering (SLS), where material is built up in layers from plastic powder fused together with a laser.
The rigid plastic components are fully articulated to create a netted structure that allows for movement. Spirals based on the Golden Ratio were applied to a computer rendering of Von Teese’s body so the garment fits her exactly.
Draped over a nude silk corset, the black-lacquered dress is cinched in at the waist and exaggerated at the shoulders, and embellished with 12,000 Swarovski crystals.
It was unveiled during an event at the Ace Hotel in New York earlier this week, as part of a showcase of products organised by 3D printing marketplace Shapeways, who printed the dress and were also behind the 3D-printed bikini we showed a couple of years ago.
Other 3D-printed fashion we’ve featured includes Iris van Herpen’s outfits shown at Paris Fashion Week. Recently 3D printing has also been used for a road-ready car design and studs for American football boots.
Photos are by Jeff Meltz unless otherwise stated.
For the first time anywhere, a work of fashion conceived and engineered in powdered nylon by the revolutionary process of 3D printing can move like a textile. On Monday evening, March 4, 2013, style icon Dita Von Teese will appear at Ace Hotel New York as a futuristic vision of the femme fatale in a gown fully realized and rendered by computers—and one that moves with all the sensuality and fluidity of its wearer. Neither pen and paper, nor needle and thread were used by designer Michael Schmidt and his high-tech collaborator Shapeways.
This groundbreaking flexible “fabric” printed straight from a computer was the result of countless hours between Mr. Schmidt and the highly expert talents of architect Francis Bitonti. “Francis was able to take my sketches for the dress, which I created specifically for Dita, and render those in the specialized language of the software,” says Mr. Schmidt. “The fluidity of the joints is all 3D-printed, layer upon layer of fine powdered nylon within the preheated chamber, based on information by the CAD file. The laser ‘sinters’ the nylon into form, a process known as select laser sintering, or SLS. It’s an articulated fabric built into the 3D print itself. It’s something that’s never been done. What Francis and Shapeways have achieved here is truly remarkable.”
That motility engineered into the sintered nylon is what sets this example of design apart from the innovative work by fashion designers who have been exploring 3D printing. Mr. Schmidt was able to realise fluidity with the very powdered nylon that has long been the hallmark of modeling by architects and industrial designers.
Forward-thinking science intersects with beauty classicism in this historic dress. “It all comes down to mathematics,” Mr. Schmidt notes, “beauty realized through mathematics.” His template was the Golden Ratio theory by 13th century theorist Fibonacci, whose formula for beauty continues to be applied by artists and scientists alike. At the core of the theory is that the spiral exists throughout nature, from a human ear to the pinecone to the galaxy.
Mr. Schmidt, in conjunction with Mr. Bitonti, applied the spiral formula to the computer rendering of the dress, in a mesh that would undulate around the body in the most feminine way possible. For this reason, Mr. Schmidt tapped longtime friend and muse Dita Von Teese, whom he deems as the consummate classical beauty. While the shape was built over a nude silk corset, most of the architecture of the silhouette, from the voluminous shoulders to the cinched waist, is the result of the hardened nylon powder. The floor-length gown moves and expands according to Ms. Von Teese’s body contours because of the netting pattern.
The printer produced 17 sections that were then hand-linked together into the dress. (Much of Mr. Schmidt’s work in sterling mesh and other materials over the years involves this time-consuming rocess.) The 3D-printed dress was then painstakingly polished and lacquered black, and then 12,000 black Swarovski crystals were hand applied to give the overall effect that finishing touch of uber glamour.
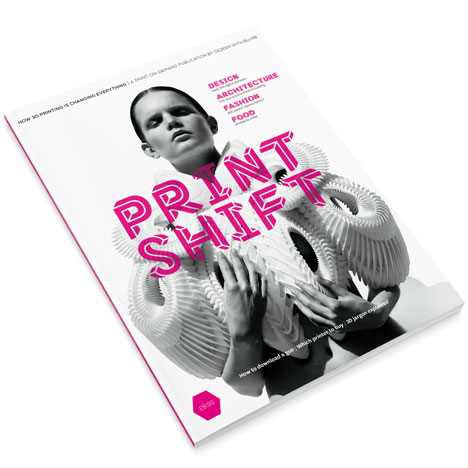
This project is featured in Print Shift, a print-on-demand magazine by Dezeen with publishers Blurb about how 3D printing is changing everything in architecture, design, fashion, food, medicine and more.
Source: Www.dezeen.com